The subject of backfocus and tilt is a very personal one. Many users design their optical train with spacers to ensure they achieve the manufacturer's recommended backfocus and trust that the installed accessories are perfectly accurate. Then by applying BlurXterminator they manage to leave the stars almost perfect.
However, there are numerous factors that contribute to minor variations.
Factors That Can Affect Back Focus, Even with Manufacturer-Recommended AccessoriesImprecision in threads: Threads are not always perfectly aligned or dimensioned, which can cause a slight misalignment in the back focus distance.
Manufacturing tolerances: Optical and mechanical components have minimal tolerances that, when accumulated, can affect the back focus distance. Even small variations in manufacturing can lead to misalignment.
Thermal expansion or contraction: Changes in temperature can affect the materials of the equipment, causing them to expand or contract, which can alter the back focus distance.
Incorrect alignment of the optical train: If the optical components are not perfectly aligned, this can cause slight displacement that affects focus.
Wear or imperfections in components: Over time, wear on threads or other elements can cause small misalignments in the optical system, affecting the back focus distance.
Tolerances in additional accessories: Even if the main accessory has the recommended back focus length, additional accessories (such as filters, adapter rings, etc.) may not have the same precision, which affects the alignment of the system.
Tolerances in Back Focus SystemsThe tolerances in optical systems depend on the specific components you're using, but in general, manufacturing tolerances for accessories like cameras, filter wheels (EFW), OAGs, and spacers are small. However, when accumulated across multiple elements, the error can become noticeable, although it’s generally still small in comparison to the total back focus length.
Estimating Tolerances
Thread Tolerance:
The threads of components like spacers, filter wheels, or adapters typically have a manufacturing tolerance that ranges from 0.05 mm to 0.1 mm. However, depending on the precision of the thread manufacturing, this tolerance can be larger in lower-quality components.
Spacer Tolerance:
Spacers are critical components with a specific length. The tolerance for spacers is generally in the range of 0.05 mm to 0.1 mm. Some high-quality spacers may have a lower tolerance, but standard spacers usually fall within this range.
Filter Wheel (EFW) Tolerance:
Tolerances in filter wheels can vary, but they are generally in the range of 0.1 mm to 0.2 mm, depending on the design and the manufacturer's quality.
OAG Tolerance:
OAGs (Off-Axis Guiders) also have some tolerance in the alignment of the guide sensor. This can be around 0.1 mm to 0.2 mm.
Camera Tolerance:
High-quality astrophotography cameras typically have a mounting tolerance in the range of 0.05 mm to 0.1 mm, although the sensor positioning tolerance may be more precise depending on the model.
Calculating the Accumulated Error
If we take a conservative tolerance estimate of 0.1 mm per component and use five components (such as camera, EFW, OAG, and two spacers), the accumulated error could be, in the worst scenario:
Accumulated Error=5×0.1 mm=0.5 mmMy Solution: Baader VariLock 46 and Baader M48 Tilter
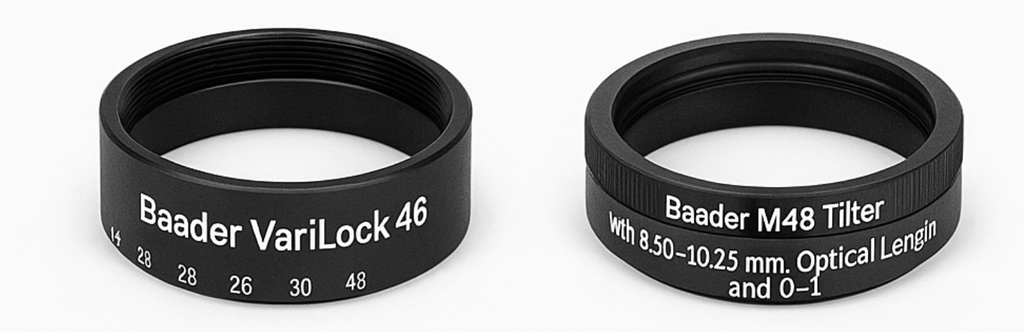
For those seeking a precise solution to these issues, the Baader VariLock 46 and Baader M48 Tilter are highly recommended accessories. The Baader VariLock 46 allows for fine adjustment of the back focus distance, while the Baader M48 Tilter helps correct tilt, ensuring that the optical train remains perfectly aligned.
These accessories not only allow for the correction of minor manufacturing defects and adjustment variations but also provide an effective way to achieve optimal optical performance by reducing the effects of small imperfections and ensuring more precise and consistent focus.
For me, the main advantage is that once installed, it allows for quick corrections without having to disassemble the optical train, allowing for rapid testing and adjustments, which allows for very rapid evaluation of problems such as vignetting, tilt, and backfocus.